Precise Control While Handling Turbine Rotor Assemblies
Handling turbine rotor assemblies requires a blend of precision engineering and innovative design. Unified Engineering rises to the challenge with custom solutions that address the unique demands of rotor tipping for large-scale projects. Our expertise ensures seamless transitions between orientations while prioritizing safety, efficiency, and versatility. Whether it’s for assembly, storage, or transport, our engineered solutions are built to meet your most demanding requirements.
The Challenge:
Handling turbine rotor assemblies, especially the transition between horizontal and vertical orientations, requires precision and specialized equipment. Existing solutions failed to accommodate the size, weight, and complexity of a 95-ton rotor assembly, necessitating the development of a custom rotor tipping fixture. This challenge was particularly critical for a large gas turbine facility in Saudi Arabia, where precise handling was essential for assembly.
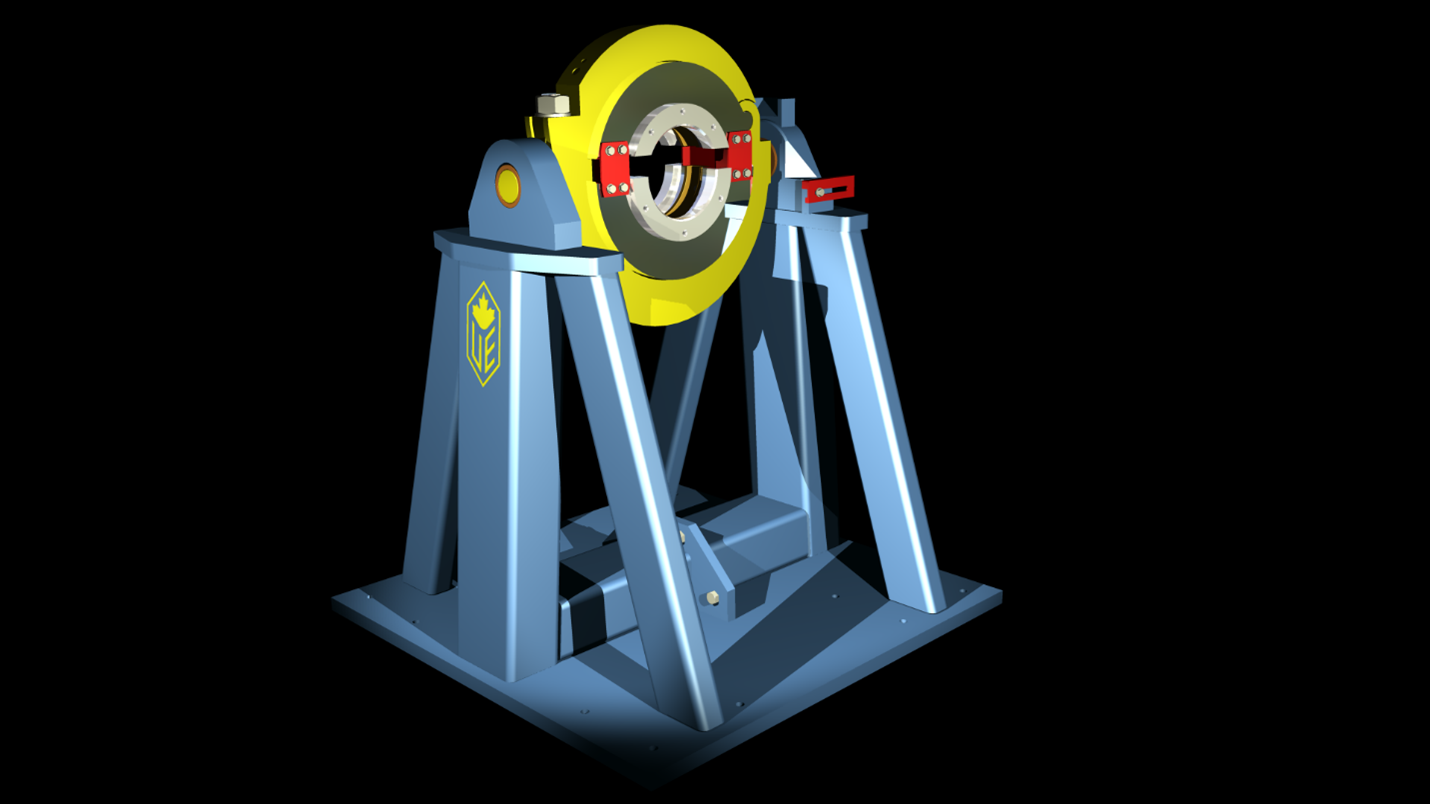

The Solution:
Unified Engineering designed and built a custom rotor tipping fixture capable of managing the weight and size of the 95-ton rotor assembly. The fixture was engineered to accommodate six different rotor sizes using a customizable clamping mechanism. Paired with an overhead crane, the fixture enabled seamless transitions between horizontal and vertical positions. The solution included a detailed operations manual for ease of use and was delivered turnkey from Ontario, Canada to Saudi Arabia.
The Benefit:
The rotor tipping fixture streamlined the turbine assembly process, ensuring safety, precision, and efficiency. Its versatile design supports multiple rotor sizes, enhancing usability for various applications. By providing a reliable, custom-built solution, Unified Engineering reduced assembly complexity and delivered a critical tool that met the unique needs of the project.